Comparison Guide: Injection Molding vs. Die Casting for Automotive Parts
Understanding Injection Molding and Die Casting
In the automotive industry, selecting the right manufacturing process for parts is crucial. Injection molding and die casting are two popular methods used for producing intricate components, each with its unique advantages and challenges. Understanding these processes can help manufacturers make informed decisions to meet their specific needs.
Injection molding involves injecting molten plastic into a mold to create parts. It is favored for its ability to produce complex shapes with a high degree of precision. Conversely, die casting involves forcing molten metal into a mold cavity under high pressure. This method is well-suited for creating strong and durable metal parts.

Material Considerations
The choice between injection molding and die casting often hinges on material requirements. Injection molding typically uses thermoplastics, which offer flexibility, lightweight properties, and resistance to corrosion. These characteristics make thermoplastics ideal for non-structural automotive components like dashboards, panels, and trims.
Die casting, on the other hand, uses metals such as aluminum, magnesium, and zinc. These materials provide excellent thermal and electrical conductivity, strength, and rigidity. As a result, die-cast parts are often used in structural components that require enhanced durability and stability, such as engine blocks and transmission housings.
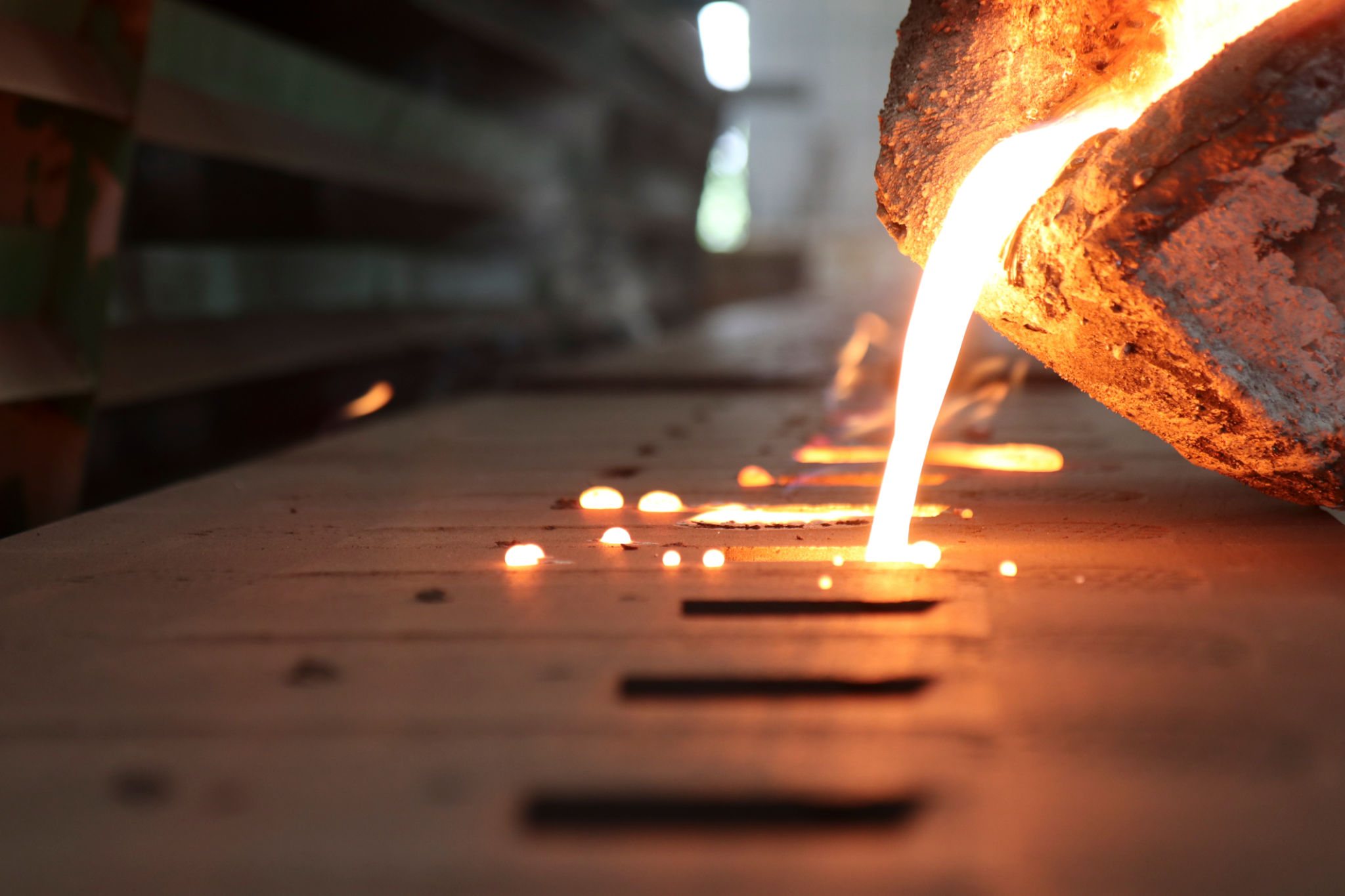
Cost Implications
When it comes to cost, several factors need consideration. Injection molding generally requires lower production costs for high-volume runs due to the relatively inexpensive price of plastic materials and efficient cycle times. The initial tooling cost can be substantial; however, the long-term savings in material costs can offset this.
In contrast, die casting involves higher initial tooling and material costs because of the metals used. However, for applications requiring metal parts, the superior strength and durability of die-cast components can justify the higher expense. Additionally, automation in die casting can significantly reduce labor costs in large-scale production.
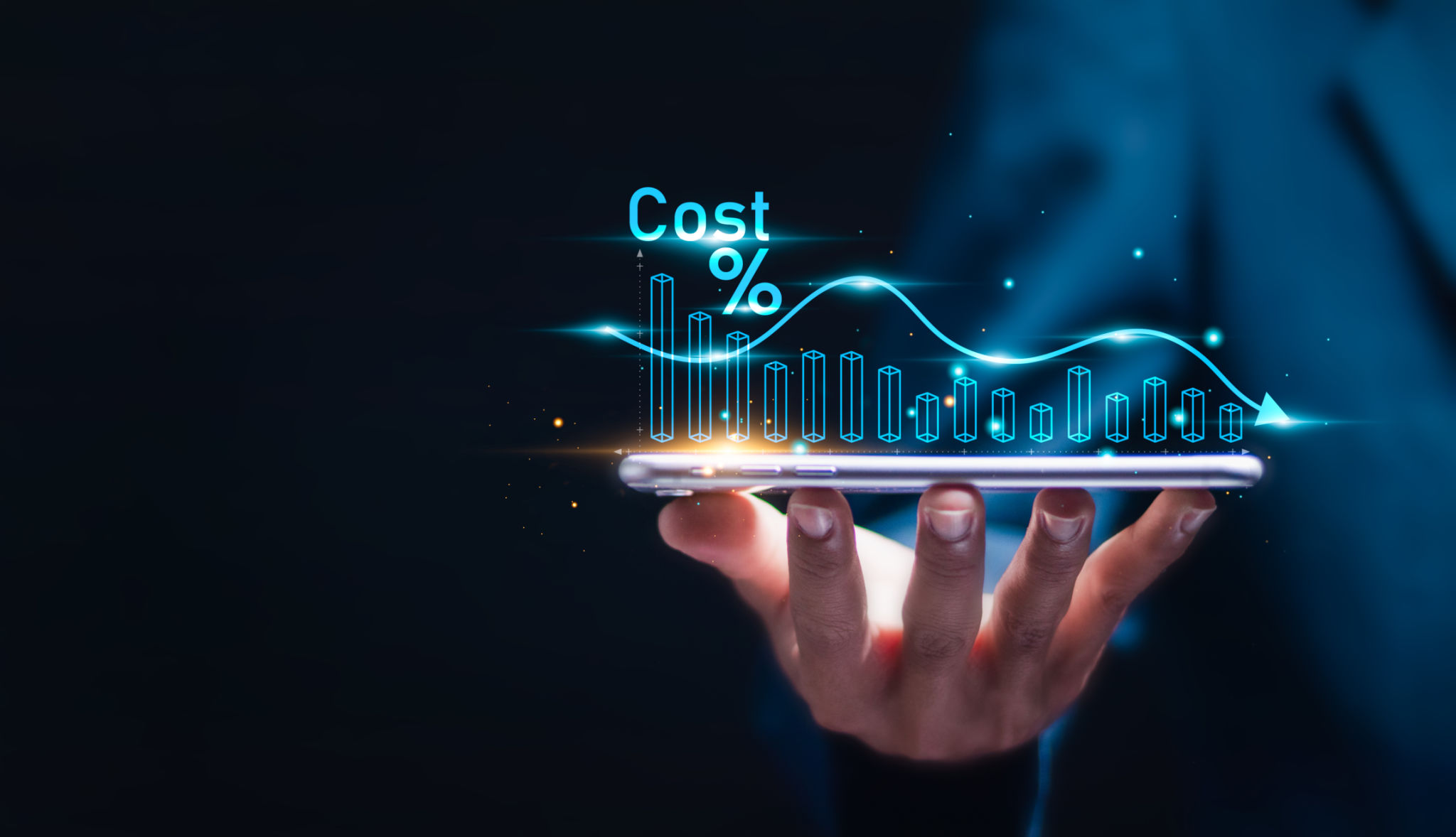
Production Speed and Efficiency
The speed of production is another critical factor when choosing between injection molding and die casting. Injection molding offers rapid cycle times, which can lead to increased throughput and efficiency, particularly beneficial for high-volume manufacturing needs.
Die casting also boasts quick production cycles thanks to advancements in automation and technology. However, the cooling time for metal parts can be longer compared to plastic, slightly impacting the overall speed. Despite this, die casting remains an efficient choice for producing large quantities of metal components swiftly.
Design Flexibility
Design flexibility is a significant advantage of injection molding. The process allows for intricate designs with tight tolerances due to the malleability of plastic materials. This flexibility enables manufacturers to innovate and adapt designs to meet evolving automotive trends without significant retooling costs.
While die casting offers less design flexibility compared to injection molding, it excels in producing complex metal parts with fine details and smooth finishes. The inherent strength of metals used in die casting also allows for thinner walls without compromising integrity, making it suitable for space-constrained applications.
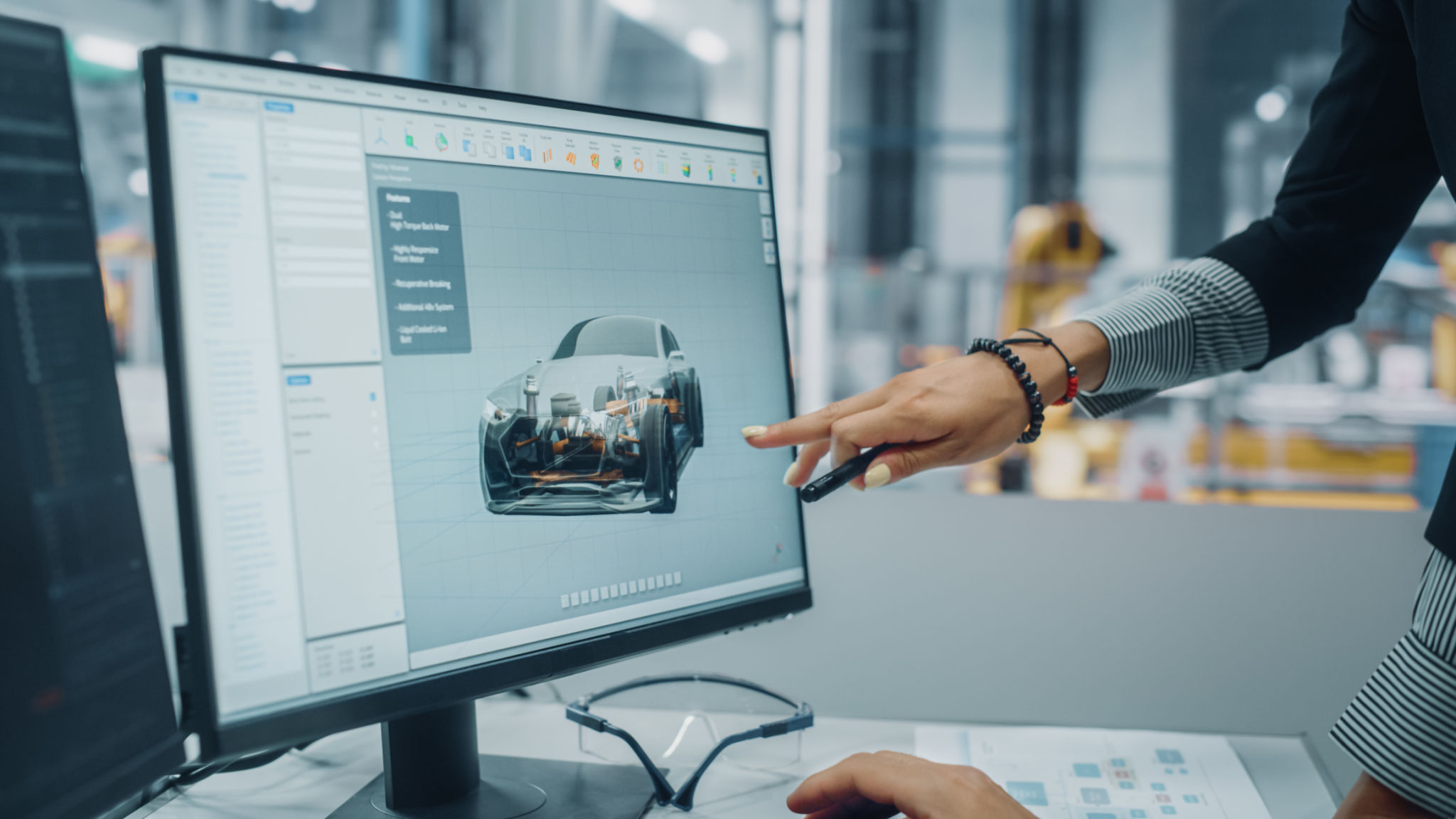
Environmental Impact
With sustainability becoming a paramount concern in the automotive industry, considering the environmental impact of manufacturing methods is crucial. Injection molding is often seen as more environmentally friendly due to the recyclability of thermoplastics and lower energy consumption during production.
Die casting's environmental impact is influenced by the recycling potential of metals like aluminum and zinc. While energy-intensive due to high temperatures required for melting metals, advancements in die-casting technology are continuously improving energy efficiency and reducing waste.
Conclusion
The choice between injection molding and die casting for automotive parts ultimately depends on specific requirements such as material properties, cost considerations, production speed, design needs, and environmental impact. By carefully evaluating these factors, manufacturers can select the most suitable process to ensure optimal performance and efficiency in their automotive components.