High-Performance Injection Molds for Automotive Needs
Understanding High-Performance Injection Molds
In the fast-paced world of automotive manufacturing, the demand for precision, efficiency, and durability in production processes is paramount. High-performance injection molds play a crucial role in meeting these demands, ensuring that automotive components are produced with exacting standards and consistency. These molds are engineered to withstand the pressures of high-volume production while maintaining the integrity of each molded part.
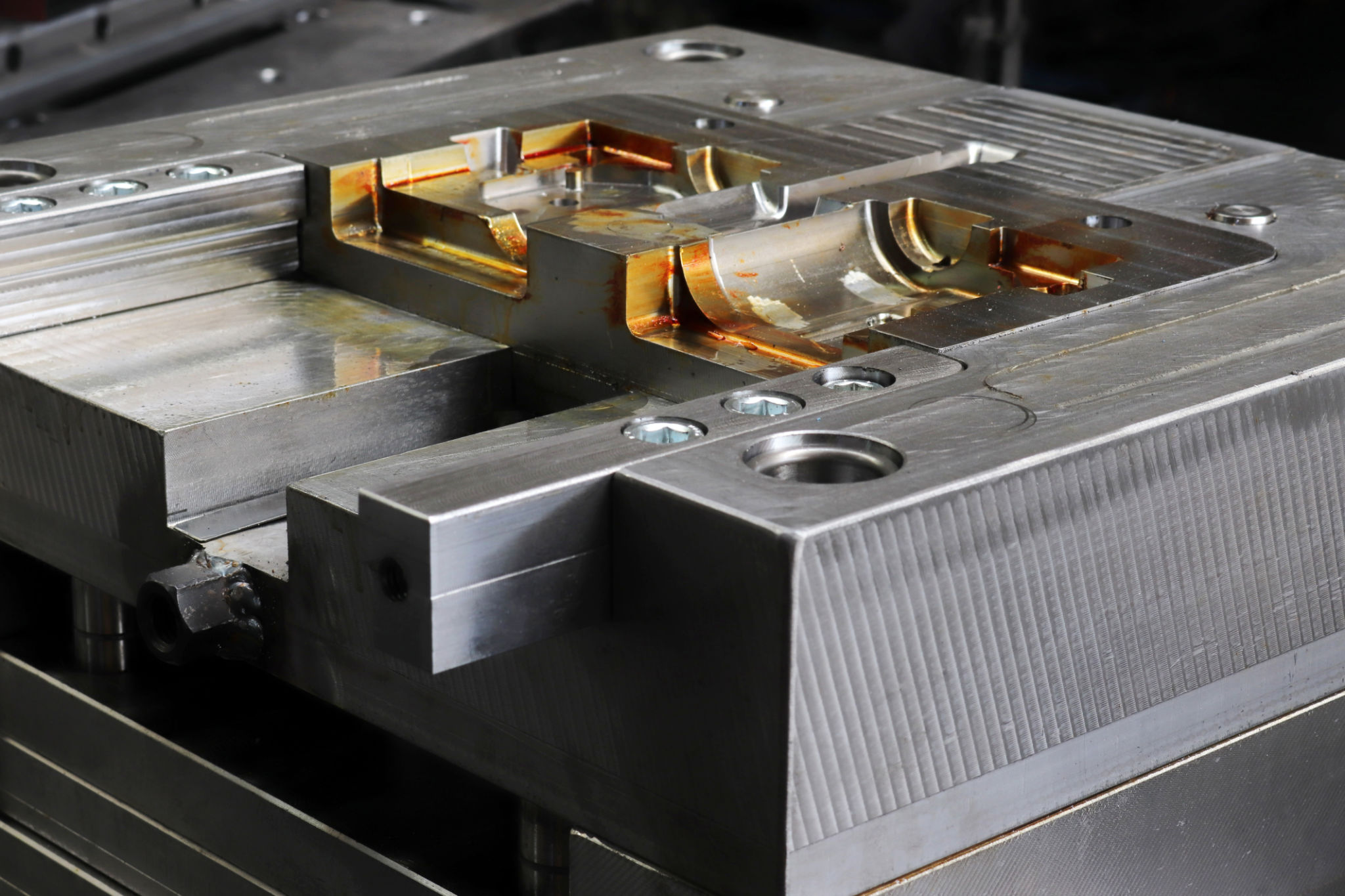
The importance of high-performance injection molds cannot be overstated, as they directly impact the quality and performance of the final automotive products. From intricate engine components to sleek interior panels, the precision of these molds determines the reliability and aesthetic appeal of vehicles on the road today.
Key Features of High-Performance Injection Molds
High-performance injection molds are distinguished by several key features that set them apart from standard molds. These features include:
- Durability: Made from high-grade steel or aluminum, these molds are designed to withstand extensive use without deforming.
- Precision: Advanced technology ensures tight tolerances and accurate dimensions for all parts.
- Efficiency: Optimized cooling systems reduce cycle times, increasing production speed without compromising quality.
By incorporating these features, manufacturers can produce components that meet stringent industry standards while reducing waste and operational costs.

Advancements in Mold Technology
The evolution of mold technology continues to push the boundaries of what is possible in automotive manufacturing. Recent advancements include the integration of computer-aided design (CAD) and computer-aided manufacturing (CAM), allowing for greater customization and flexibility in mold design. Additionally, the use of 3D printing for prototyping has accelerated the development process, enabling rapid iterations and improvements.
These technological innovations have not only enhanced the precision and efficiency of injection molds but have also expanded the range of materials that can be effectively utilized, including new lightweight composites and reinforced polymers.
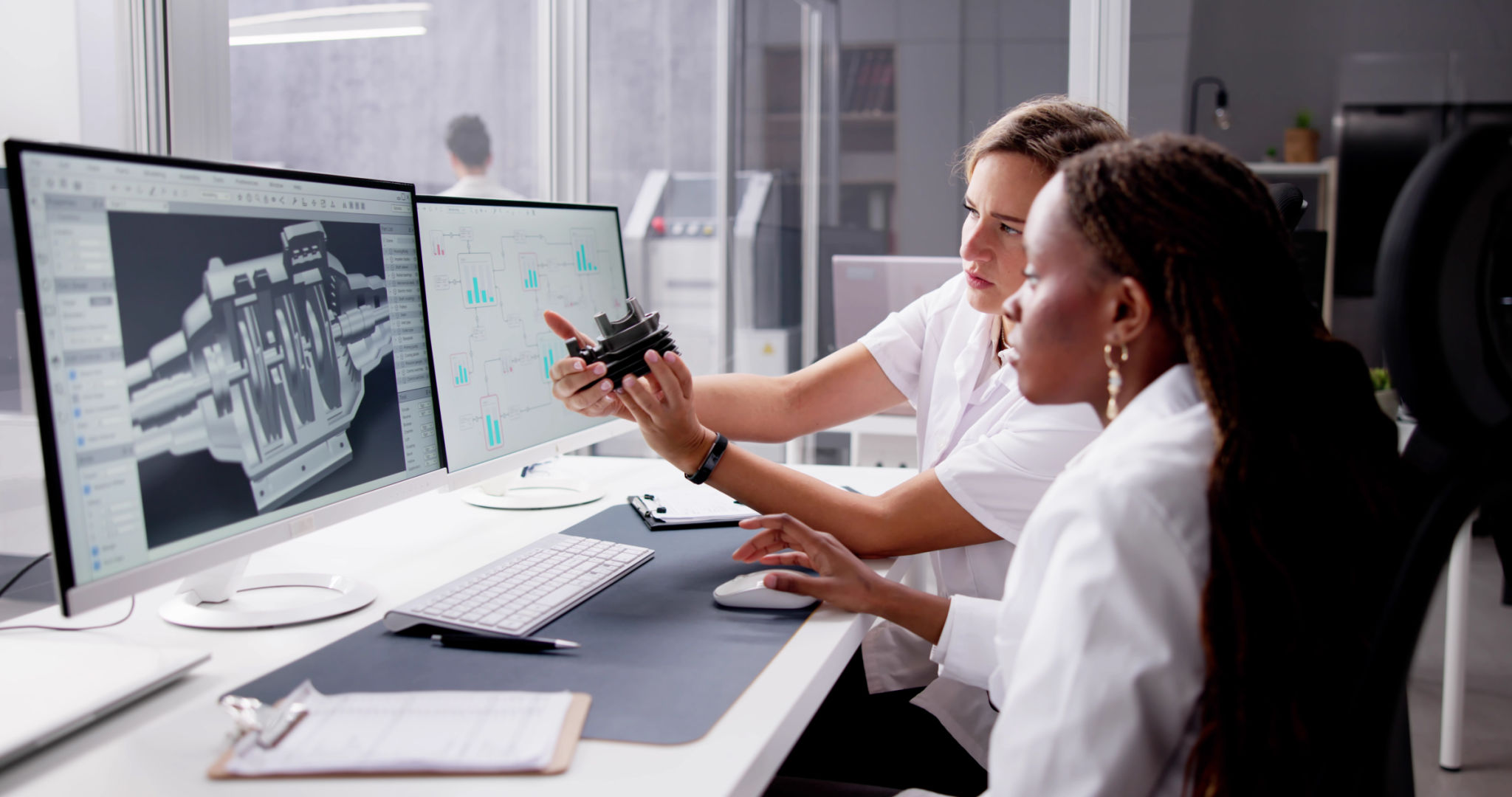
Applications in the Automotive Industry
High-performance injection molds are integral to several critical applications within the automotive industry. They are used to produce a vast array of components, ranging from exterior body panels to complex under-the-hood parts. Some notable applications include:
- Dashboard and Interior Trim: Ensuring a seamless fit and finish for aesthetic appeal.
- Bumpers and Grilles: Providing strength and resilience against environmental forces.
- Engine Components: Offering precision for optimal engine performance.
Each application demands specific mold characteristics, underscoring the need for advanced mold engineering tailored to individual component requirements.
Future Trends in Injection Molding
As the automotive industry continues to evolve, high-performance injection molds will play a pivotal role in supporting new trends. The shift towards electric vehicles (EVs) and autonomous driving technologies will demand even more sophisticated molding techniques to accommodate innovative design requirements and materials.
Sustainability is another emerging trend, with manufacturers seeking environmentally friendly production methods. This includes developing molds that minimize material waste and energy consumption during production processes.
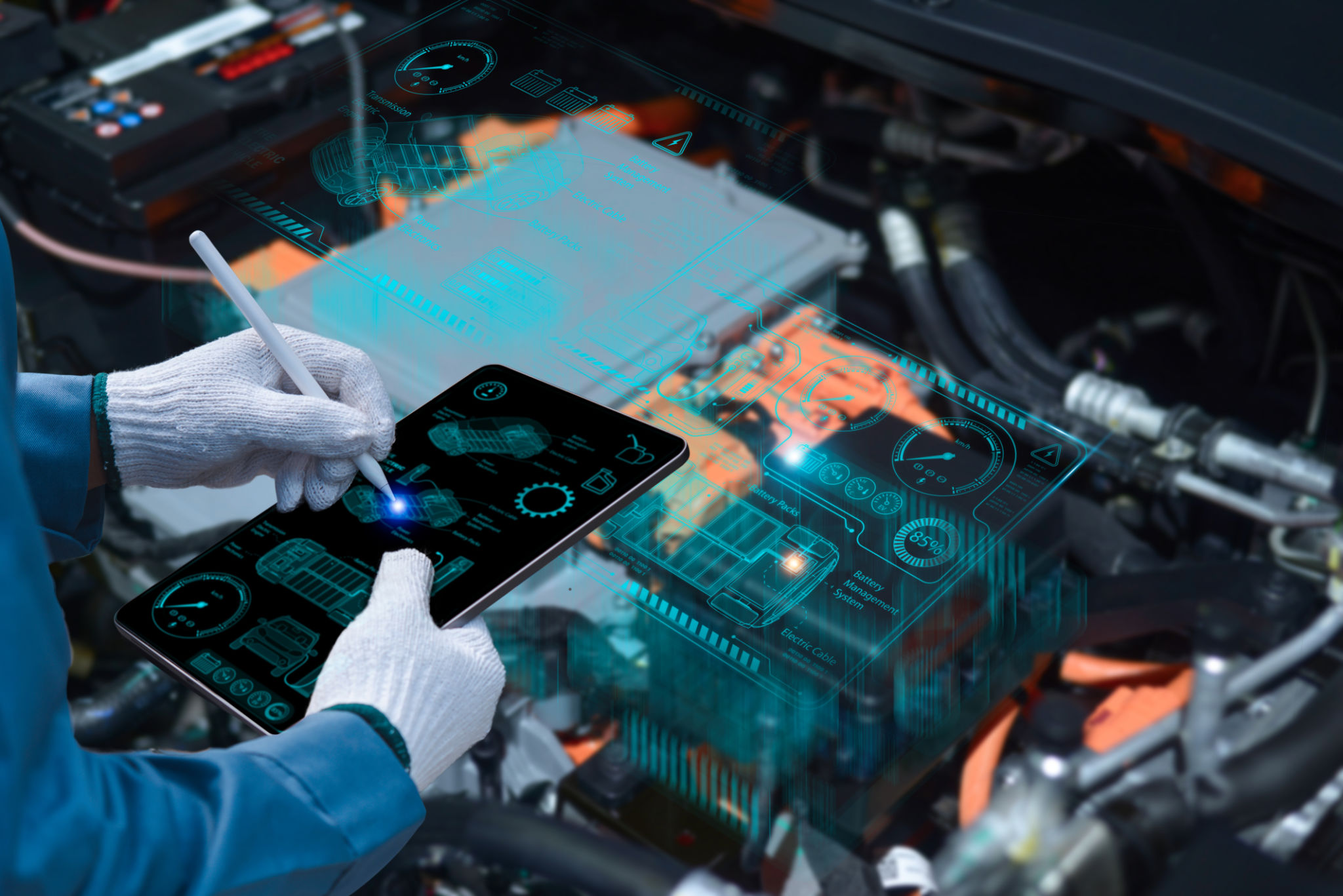
Conclusion: The Road Ahead
The future of automotive manufacturing is intricately linked to advancements in high-performance injection molds. As technology progresses, these molds will continue to enable manufacturers to produce high-quality, reliable components efficiently. By staying at the forefront of mold technology, automotive companies can ensure they meet the demands of a rapidly changing industry, delivering vehicles that are both innovative and sustainable.
In conclusion, high-performance injection molds are not just a component of manufacturing; they are a cornerstone of modern automotive innovation, driving quality and efficiency to new heights.